3 Easy Facts About Alcast Company Described
3 Easy Facts About Alcast Company Described
Blog Article
The Only Guide to Alcast Company
Table of ContentsAlcast Company - QuestionsAlcast Company Can Be Fun For EveryoneEverything about Alcast CompanyGet This Report about Alcast CompanySome Ideas on Alcast Company You Need To KnowAlcast Company Can Be Fun For Anyone
The refined difference depends on the chemical material. Chemical Contrast of Cast Aluminum Alloys Silicon advertises castability by lowering the alloy's melting temperature and enhancing fluidness throughout spreading. It plays a vital role in permitting elaborate molds to be filled up precisely. Furthermore, silicon contributes to the alloy's stamina and put on resistance, making it valuable in applications where durability is crucial, such as vehicle parts and engine parts.It additionally boosts the machinability of the alloy, making it easier to refine into ended up products. By doing this, iron adds to the total workability of aluminum alloys. Copper enhances electrical conductivity, making it useful in electrical applications. It also enhances corrosion resistance and contributes to the alloy's total strength.
Manganese contributes to the strength of light weight aluminum alloys and enhances workability (Foundry). It is generally used in wrought light weight aluminum products like sheets, extrusions, and profiles. The visibility of manganese help in the alloy's formability and resistance to cracking during fabrication procedures. Magnesium is a lightweight element that provides strength and effect resistance to aluminum alloys.
Alcast Company - The Facts
Zinc enhances the castability of light weight aluminum alloys and assists regulate the solidification procedure during casting. It boosts the alloy's toughness and solidity.
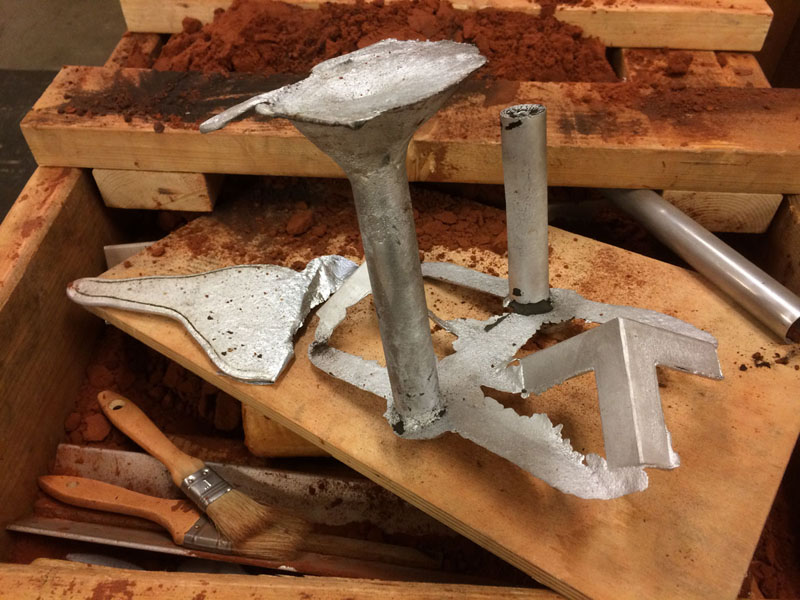
The primary thermal conductivity, tensile stamina, yield toughness, and elongation vary. Amongst the above alloys, A356 has the greatest thermal conductivity, and A380 and ADC12 have the most affordable.
Getting The Alcast Company To Work

The 25-Second Trick For Alcast Company
Its distinct properties make A360 a useful selection for precision casting in these sectors, improving item sturdiness and high quality. Aluminum alloy 380, or A380, is a widely used spreading alloy with a number of distinct characteristics. It offers excellent castability, making it an excellent option for precision casting. A380 exhibits excellent fluidity when molten, guaranteeing complex and detailed molds are properly recreated.
In precision casting, light weight aluminum 413 shines in the Consumer Electronics and Power Tools sectors. This alloy's remarkable rust resistance makes it an exceptional option for outdoor applications, ensuring durable, sturdy products in the stated industries.
The Basic Principles Of Alcast Company
The light weight aluminum alloy you pick will significantly influence both the spreading procedure and the properties of the last item. Due to the fact that of this, you should make your choice carefully and take an informed method.
Identifying the most ideal light weight aluminum alloy for your application will certainly indicate evaluating a wide variety of qualities. The initial group addresses alloy attributes that affect the production process.
A Biased View of Alcast Company
The alloy you choose for die casting straight impacts a number of facets of the spreading process, like how easy the alloy is to collaborate with and if it is susceptible to casting problems. Warm breaking, also recognized as solidification splitting, is a regular die casting defect for light weight aluminum alloys that can cause internal or surface-level rips or cracks.
Specific light weight aluminum alloys are extra prone to hot splitting than others, and your option needs to consider this. It can harm both the actors and the die, so you need to look for alloys with high anti-soldering residential or commercial properties.
Corrosion resistance, which is already a remarkable quality of light weight aluminum, can differ considerably from alloy to alloy and is an essential particular to consider depending on the environmental problems your product will certainly be exposed to (Aluminum Casting). Put on resistance is an additional residential or commercial property frequently sought in light weight aluminum items and can distinguish some alloys
Report this page